FANUC Servo Amplifier Alarm Codes List
FANUC servo amplifier alarm codes are critical for diagnosing issues in CNC machines and robotic systems. These codes help identify problems related to the servo amplifier, motor, or associated components. Below is a list of FANUC servo amplifier alarms and faults with a short description briefly describing the source of each error code. Some point to the source of the problem itself, others point to the problem and do not identify the failing/malfunctioning component.
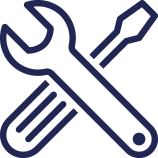
Servo Amplifier We Service
FANUC Alpha | FANUC AC Digital & Analog | FANUC AC Serial Interface | FANUC AC Series i & S
Instant Service Quotes
Search your FANUC parts number for an instant repair or exchange quote. We provide a fault diagnosis and a dependable 1-year warranty.
400 Alarms 600 Alarms Beta is 6130 Alarms SVPMi (6134, 6230) Alarms
Fanuc Servo Amplifier Alarms
Alarm Code | Description | Next Steps |
---|---|---|
Amplifier is not ready or commanded to run |
||
IPM alarm for L–and M–axis axes |
||
Amplifier is ready (normal operating state) |
||
DC voltage of the main circuit power supply is abnormally high. |
||
Internal cooling circuit faulty. |
||
+5 VDC of the control circuit power supply is abnormally low. |
||
DC voltage of the main circuit power supply is abnormally low or the circuit breaker is tripped. |
||
DC voltage (DC link) has dropped |
||
Average regenerative discharge energy is too high (too frequent acceleration/deceleration) |
||
A communication error for the serial pulse coder was detected. |
||
Excessive regenerative discharge alarm. |
||
Inverter: Overheat |
||
Inverter: Overheat |
||
Inverter: Fuse blown |
||
Inverter: Overheat |
||
Fan Alarm (Fan is Stopped) |
||
Input power supply under-voltage (UV) |
||
Inverter: IPM alarm (M axis) |
||
When the absolute pulse coder is used, the motor has not yet rotated through more than one turn after the first power–up. |
||
The main circuit power supply has an open phase. |
||
The DC link voltage is abnormally high. |
||
An error occurred in internal parameter data transfer processing. |
||
The frequency of the main circuit input power supply is abnormal. |
||
The input power supply of the main circuit has an imbalance. |
||
When the magnetic contactor is turned on, the phase sequence of the power supply cannot be determined. |
||
A parameter has been specified incorrectly. Abnormal current alarm (N axis) External cooling circuit faulty. |
||
Inverter: IPM alarm (N axis) |
||
ROM is faulty. |
||
RAM is faulty |
||
A software is not operating normally. |
||
Abnormal current alarm (L axis) Abnormally high current in the L–and M–axis motors DC link current alarm (L axis) |
||
IPM alarm for L–and M–axis axes. |
||
Breaker has tripped |
||
An overcurrent alarm or IPM alarm DC link current alarm (M axis) |
||
Faulty cooling circuit |
||
Abnormal current alarm (N axis) DC link current alarm N axis) |
||
Discharge alarm |
||
The regenerative discharge circuit may be faulty |
||
An error was detected in the RAM write/read test at power–up. The input power supply is abnormal (open phase). |
||
External cooling circuit faulty |
||
The temperature of the regenerative resistor has risen abnormally. (PSMR) |
||
High current flow the the main circuit of that axis has occurred |
||
High current alarm L axis |
||
High current alarm M axis |
||
High voltage alarm |
||
DC voltage of the power circuit for that axis is high |
||
The regenerative discharge unit has overheated |
||
FSSB communication error |
||
Low voltage alarm |
||
The circuit voltage is unusually low |
||
200-V control power (CX1A) is not supplied. Alternatively, the 24-VDC power is short-circuited. |
||
Overheat alarm |
||
Current exceeding the preset value has continued longer than normal. |
||
Communication error between amplifier and module DC link low voltage alarm |
||
Feedback and velocity command mismatch |
||
A parameter that requires power–down has been specified. FSSB communication error |
||
A first to third reference position return cannot be executed because the reference position has not yet been established. |
||
DC link overvoltage alarm |
Fanuc Servo Amplifier 400 Alarm Codes
Alarm Code | Message | Description | Next Steps |
---|---|---|---|
SERVO ALARM: n–TH AXIS OVERLOAD |
The n–th axis (axis 1–8) overload signal is on. Refer to diagnostic display No. 201, 720 or 721 for details. |
||
SERVO ALARM: n–TH AXIS VRDY OFF |
The n–th axis (axis 1–8) servo amplifier READY signal (DRDY) went off. |
||
SERVO ALARM 3, 4TH AXIS OVERLOAD |
3-axis, 4-axis overload signal is on. Refer to diagnostic display 722 or 723 for details. |
||
SERVO ALARM: n–TH AXIS VRDY ON |
Even though the n–th axis (axis 1–8) READY signal (MCON) went off, the servo amplifier READY signal (DRDY) is still on. Or, when the power was turned on, DRDY went on even though MCON was off. Check that the servo interface module and servo amp are connected. |
||
SERVO ALARM: (ZERO POINT RETURN FAULT) |
Position control system fault. Due to an NC or servo system fault in the reference position return, there is the possibility that reference position return could not be executed correctly. Try again from the manual reference position return. |
||
SERVO ALARM: EXCESS ERROR |
The difference in synchronous axis position deviation exceeded the set value. |
||
SERVO ALARM: n AXIS TORQUE ALM |
Abnormal servo motor load has been detected. Alternatively, abnormal spindle motor load has been detected in Cs mode. |
||
SERVO ALARM: n–TH AXIS – EXCESS ERROR |
The position deviation value when the n–th axis (axis 1–8) stops is larger than the set value. |
||
SERVO ALARM: n–TH AXIS – EXCESS ERROR |
The position deviation value when the n–th axis (axis 1–8) moves is larger than the set value. |
||
SERVO ALARM: n–th AXIS – LSI OVERFLOW |
The contents of the error register for the n–th axis (axis 1–8) exceeded 2^31 power. This error usually occurs as the result of an improperly set parameters. |
||
SERVO ALARM: n–TH AXIS – DETECTION RELATED ERROR |
N–th axis (axis 1–8) digital servo system fault. Refer to diagnosis display No. 200 and No.204 for details. Also look at the servo amplifier for alarm code. |
||
SERVO ALARM: n–TH AXIS – EXCESS SHIFT |
A speed higher than 511875 units/s was attempted to be set in the n–th axis (axis 1–8). This error occurs as the result of improperly set CMR. |
||
SERVO ALARM: n–TH AXIS – DISCONNECTION |
Position detection system fault in the n–th axis (axis 1–8) pulse coder (disconnection alarm). Refer to diagnosis display No. 201 for details. |
||
SERVO ALARM: n–TH AXIS – PARAMETER SETTING ERROR |
The n–th axis (axis 1–8) parameter setting is faulty. (A servo motor or pulse coder not used by this system has been set.) |
||
SERVO ALARM: n AXIS SYNC TORQUE (M series) |
During simple synchronous control, the difference between the torque commands for the master and slave axes exceeded the value set in parameter No. 2031. |
||
SERVO ALARM: n AXIS EXCESS ER (D) |
The difference between the errors in the semi–closed loop and closed loop has become excessive during dual position feedback. Check the values of the dual position conversion coefficients in parameters No. 2078 and 2079. |
||
SERVO ALARM: n AXIS |
In torque control of PMC axis control, a specified allowable speed has been exceeded. |
||
SERVO ALARM: n AXIS |
In torque control of PMC axis control, the parameter–set allowable cumulative travel distance has been exceeded. |
||
n AXIS : SV. MOTOR OVERHEAT |
A servo motor overheat occurred. |
||
n AXIS : CNV. OVERLOAD |
1) PSM: Overheat occurred. 2) β series SVU: Overheat occurred. |
||
n AXIS : CNV. LOWVOLT CON. |
1) PSM: The control power supply voltage has dropped. 2) PSMR: The control power supply voltage has dropped. 3) β series SVU: The control power supply voltage has dropped |
||
n AXIS : INV. LOWVOLT CONTROL |
SVM: The control power supply voltage has dropped. |
||
n AXIS : INV. LOWVOLT DC LINK |
SVM: The DC link voltage has dropped. |
||
n AXIS : SOFTTHERMAL (OVC) |
The digital servo software detected the soft thermal state (OVC). |
||
n AXIS : CNV. OVERCURRENT POWER |
PSM: Overcurrent flowed into the input circuit. |
||
n AXIS : INV. ABNORMAL CURRENT |
1) SVM: The motor current is too high. 2) α series SVU: The motor current is too high. 3) β series SVU: The motor current is too high. |
||
n AXIS : CNV. OVERVOLT POWER |
1) PSM: The DC link voltage is too high. 2) PSMR: The DC link voltage is too high. 3) α series SVU: The C link voltage is too high. 4) β series SVU: The link voltage is too high. |
||
n AXIS : CNV. EX DECELERATION POWER |
1) PSMR: The regenerative discharge amount is too large. 2) α series SVU: The regenerative discharge amount is too large. Alternatively, the regenerative discharge circuit is abnormal. |
||
n AXIS : ABNORMAL CURRENT OFFSET |
The digital servo software detected an abnormality in the current offset. |
||
n AXIS : CURRENT OFFSET |
The digital servo software detected an abnormality in the current offset at power–on or during operation. |
||
n AXIS : EXCESS |
The digital servo software detected an abnormal current. |
||
n AXIS : DETECTION |
The digital servo software detected an abnormal current at power–on or during operation. |
Fanuc Servo Amplifier 600 Alarm codes
Alarm Code | Message | Description | Next Steps |
---|---|---|---|
n AXIS: INV. DC LINK OVER CURRENT |
DC link current is too large. |
||
n AXIS: INV. RADIATOR FAN FAILURE |
The external dissipator cooling fan failed. |
||
n AXIS: INV. OVERHEAT |
The servo amplifier was overheated. |
||
n AXIS: INV. IPM ALARM(OH) |
The IPM (intelligent power module) detected an overheat alarm. |
||
n AXIS: AMP. COMMUNICATION ERROR |
Communication between the SVM and the PSM failed. |
||
n AXIS: CNV. EX. DISCHARGE POWER |
PSMR: Regenerative power is too large. |
||
n AXIS: CNV. RADIATOR FAN FAILURE |
PSM: The external dissipator cooling fan failed. PSMR: The external dissipator cooling fan failed. |
||
n AXIS: CNV. SINGLE PHASE FAILURE |
PSM: Input voltage is in the open–phase condition. PSMR: Input voltage is in the open–phase condition. |
Fanuc Servo Amplifier Beta is 6130 Alarms
Alarm Code | Description | Next Steps |
---|---|---|
Invalid digital servo parameter setting |
||
Pulsecoder phase error (built-in) |
||
Soft phase alarm (built-in) |
||
LED error (built-in) |
||
Pulse error (built-in) |
||
Count error (built-in) |
||
Serial data error (built-in) |
||
Data transfer error (built-in) |
||
LED error (separate) |
||
Pulsecoder phase error (separate) |
||
Count error (separate) |
||
Pulse error (separate) |
||
Soft phase alarm (separate) |
||
Serial data error (separate) |
||
Data transfer error (separate) |
||
Sensor error (separate) |
||
Invalid parameter |
||
Excessive semi-full error |
||
Servo motor overheat |
||
Converter: control power supply undervoltage |
||
Converter: DC link undervoltage |
||
Soft thermal (OVC) |
||
Inverter: motor current alarm |
||
Converter: DC link overvoltage |
||
Converter: Excessive deceleration power |
||
Current offset error |
||
Inverter: internal cooling fan stopped or circuit failed |
||
Soft disconnection alarm |
||
Hard disconnection alarm (separate) |
||
Feedback mismatch alarm |
||
Inverter: IPM alarm |
||
Soft disconnection alarm (α Pulsecoder) |
||
Inverter: cooling fan stopped of the radiator |
||
Inverter: IPM alarm (OH) |
FANUC Servo Amplifier SVPMi (6134, 6230)
Status 1 Spindle Unit | Status 2 Spindle Unit | Description | Next Steps |
---|---|---|---|
Communication data alarm |
Details & Solutions | ||
Converter: control power supply low voltage |
Details & Solutions | ||
- (dash) |
Power supply voltage decrease |
Details & Solutions | |
Communication error between amplifier and module |
Details & Solutions | ||
- (dash) |
Input power supply is abnormal (open phase) |
Details & Solutions | |
- (dash) |
DC voltage at the DC link is abnormally high |
Details & Solutions | |
IPM alarm |
Details & Solutions | ||
Excessive offset of the phase U current detection circuit |
Details & Solutions | ||
Excessive offset of the phase V current detection circuit |
Details & Solutions | ||
Position sensor polarity setting incorrect |
Details & Solutions | ||
Serial transfer data error |
Details & Solutions | ||
Position coder disconnected |
Details & Solutions | ||
Short-period overload |
Details & Solutions | ||
Overcurrent in the converter input circuit |
Details & Solutions | ||
- (dash) |
The main circuit power module (IPM) has detected an abnormal condition. |
Details & Solutions | |
Motor lock alarm |
Details & Solutions | ||
Serial communication LSI RAM error |
Details & Solutions | ||
- (dash) |
The main circuit capacitor was not recharged within the specified time |
Details & Solutions | |
Converter: DC link precharge failure |
Details & Solutions | ||
Parameter data out of the specifiable range |
Details & Solutions | ||
Gear ratio parameter error |
Details & Solutions | ||
Speed detector parameter error |
Details & Solutions | ||
Position coder one-rotation signal detection error |
Details & Solutions | ||
Position coder one-rotation signal not detected |
Details & Solutions | ||
Position coder signal error |
Details & Solutions | ||
Excessive speed command calculation value during spindle synchronization |
Details & Solutions | ||
Converter: DC link undervoltage |
Details & Solutions | ||
51 |
- (dash) |
In the main circuit, the DC voltage (DC link) has dropped. |
Details & Solutions |
ITP signal error I |
Details & Solutions | ||
ITP signal error II |
Details & Solutions | ||
Current overload alarm |
Details & Solutions | ||
Converter: main circuit overload |
Details & Solutions | ||
58 |
- (dash) |
Temperature of the main circuit heat sink has risen abnormally |
Details & Solutions |
59 |
- (dash) |
Internal cooling circuit faulty |
Details & Solutions |
Motor sensor disconnected |
Details & Solutions | ||
CRC test alarm |
Details & Solutions | ||
Abnormal initial test operation |
Details & Solutions | ||
Motor sensor one-rotation signal detection error |
Details & Solutions | ||
Motor sensor one-rotation signal not detected |
Details & Solutions | ||
Motor sensor signal error |
Details & Solutions | ||
Spindle sensor disconnected |
Details & Solutions | ||
Spindle sensor one-rotation signal detection error |
Details & Solutions | ||
Spindle sensor one-rotation signal not detected |
Details & Solutions | ||
Spindle sensor signal error |
Details & Solutions |