A06B-6102-H245 FANUC SPM-45 TYPE 1
FANUC parts >> A06B-6102-H245 FANUC SPM-45 TYPE 1
Part Name: FANUC SPM-45 TYPE 1
Part Number: A06B-6102-H245
Exchange Price
$3,848
Need this part? Call for availability. If inventory allows, we will convert an item in stock.
Refurbished Repair Price
$3,587
Standard Repair Price
$3,251
Turnaround times for standard repairs are based on workload. Please contact Tri Star CNC Services for emergency repair requirements.
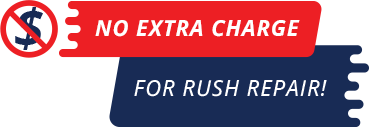
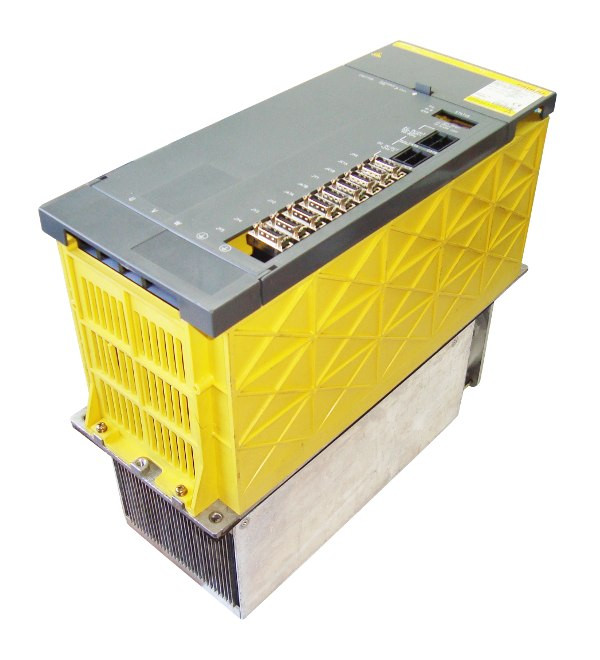
A06B-6102-H245 FANUC SPM-45 TYPE 1 Repair & Parts Exchange
Phone Support
For help resolving an issue with your A06B-6102-H245 FANUC SPM-45 TYPE 1 part, give us a call for Phone support. Our technicians are standing by to walk you through machine repairs at no cost. If you need professional repairs for your FANUC CNC parts, we'll walk you through the send-in process to minimize downtime. Call us today for Phone support for your FANUC machine.
FANUC CNC Parts Repair and Replacement Services
Get repairs for your A06B-6102-H245 FANUC SPM-45 TYPE 1 part by sending your parts to Tri Star CNC. We always thoroughly inspect, repair and clean your parts before sending them back. To get started, fill out an RMA form and send it along with a contact form. You only pay for the necessary services we perform, so if your part only needed to be cleaned to continue functioning, you'll only be charged for that service. We'll also replace your A06B-6102-H245 FANUC SPM-45 TYPE 1 part when it has reached the end of its lifecycle.
Tri Star CNC offers the best selection of FANUC replacement parts. When your part has broken, it will put your whole production process on hold. We have the fastest repair turnaround rate, so we’ll have you back up and running as fast as possible. If you still don’t have time to spare, we can send you a replacement part to move the process along even faster.
Field Service
Our send-in repair services are available for all locations within the U.S. Consult our field service map to see whether on-site maintenance for your A06B-6102-H245 FANUC SPM-45 TYPE 1 part is available.
We provide the following services for all FANUC parts:
Alarm Code Directory
Seeing an alarm code on your FANUC CNC machine? Don't worry! Check out our comprehensive error list to diagnose your problem.
Contact Tri Star CNC Services for the fastest repairs & replacement for CNC parts.
Parts & Repair Warranty Information
Exchange parts and refurbished repairs carry a one year “bumper to bumper” warranty covering labor and all circuits in the unit.
Standard repairs carry a one-year limited warranty covering the repaired circuit and associated labor.